Die Maske aus Eschelbach geht als Qualitätsprodukt an den Markt
Keine Maske für die schnelle Mark: Die Idee, ins Maskengeschäft einzusteigen, hatte Alexander Nägele kurz vor dem ersten Lockdown.
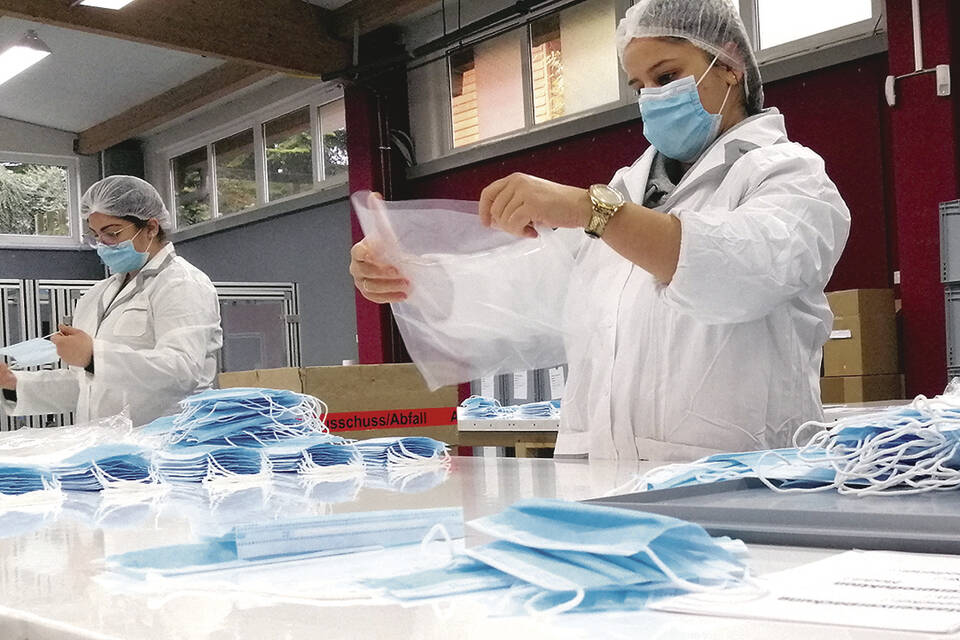
Von Tim Kegel
Sinsheim-Eschelbach. Pff-tsch-pff-tsch-pff-tsch-pff-tsch. Immer wieder. Ein monotones, hydraulisches Geräusch aus Abwickeln, Kleben, Pressen und Stanzen liegt über der Halle. Mund-Nasenschutz tragendes Personal in klinischen Kitteln konfektioniert an einem Packtisch Mund-Nase-Masken: "Made in Germany – Produced in Sinsheim" steht auf der Packung.
"Das
- Alle Artikel lesen mit RNZ+
- Exklusives Trauerportal mit RNZ+
- Weniger Werbung mit RNZ+